11 - MAINTENANCE OPERATIONS
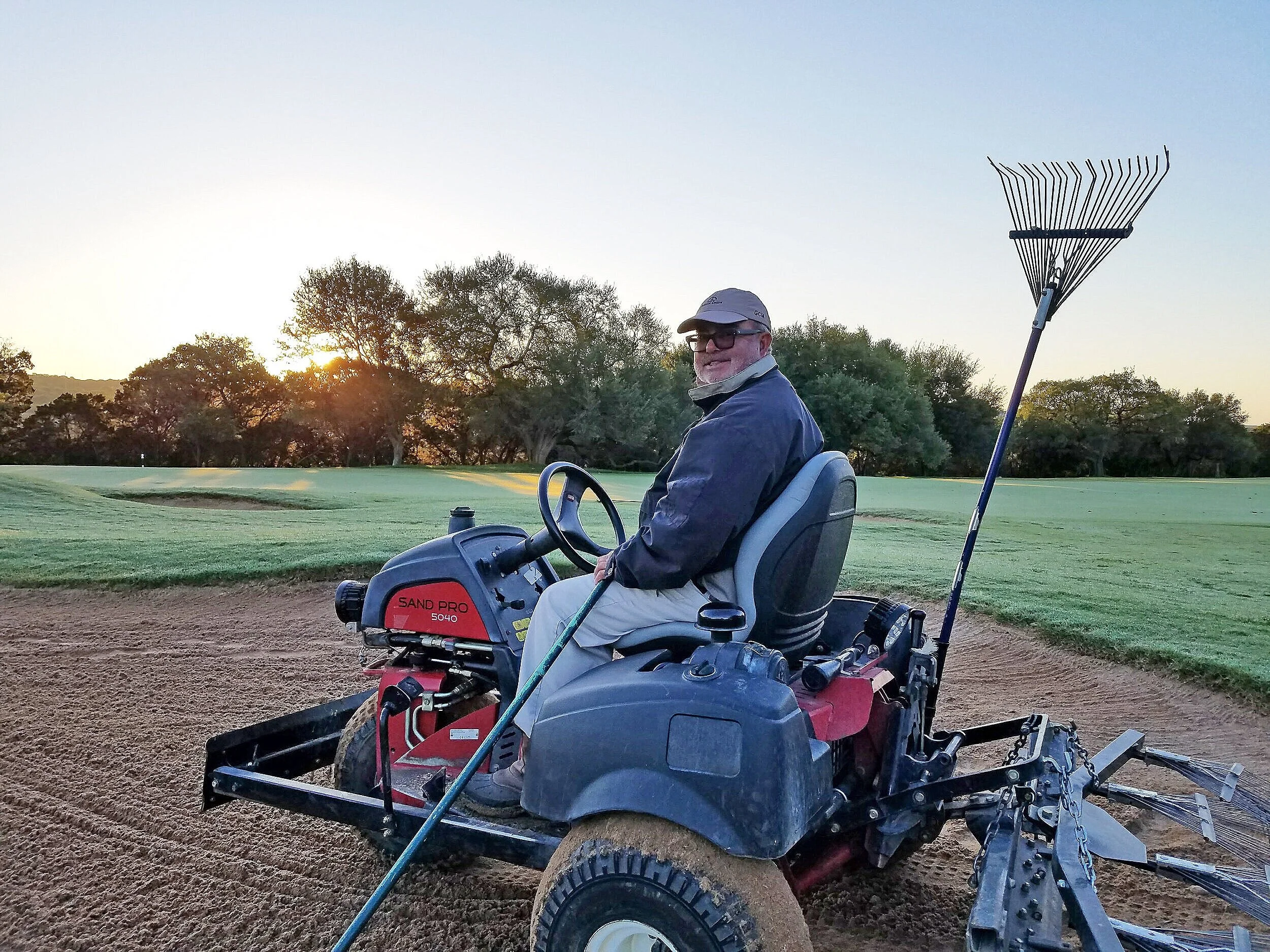
Maintenance operations facilities include areas for employee training, equipment maintenance, and storage of all maintenance items including chemicals, fertilizers, and fuel. Key protocols must be put in place to minimize environmental impact and promote the health and safety of staff and customers.
Regulatory Considerations
Early engagement amongst developers, designers, community groups, and permitting agencies is essential to constructing a golf maintenance and storage facility. Local and regional regulations may be in place by municipality or county. Consult the proper regulatory officials to determine requirements.
It is important to ensure proper handling and storage of pesticides and petroleum-based products to reduce human, environmental, and economic risks including the potential for serious injury to operators or bystanders, environmental contamination, fines, and cleanup costs. Resources for state regulations are noted in each subsection.
Labor regulations and guidance pertain to wages, work hours, licenses, safety training, and more. Every employer shall post in a conspicuous place upon its premises, a workplace poster regarding federal and state laws. Requirements may be found at: https://www.twc.texas.gov/businesses/posters-workplace
Additional resources:
Texas’ statewide recycling program, governed by the TQEC: https://www.tceq.texas.gov/p2/recycle
The Texas Workforce Commission enforces regulations on wages, hour requirements, and licenses: https://www.twc.texas.gov/equal-opportunity-law
Texas Civil Rights and Discrimination: https://www.twc.texas.gov/partners/civil-rights-discrimination
OSHA training: https://www.osha.gov/training/outreach
GCSAA labor guidance: https://www.gcsaa.org/advocacy/compliance/labor
Department of Labor youth and labor: https://www.dol.gov/general/topic/youthlabor
Texas Emergency Contact Numbers
Poison Control Center: 1-800-222-1222 (National)
State of Texas Spill-Reporting Hotline and the SERC: 1-800-832-8224—24 hours a day. https://www.tceq.texas.gov/response/serc.html
TCEQ Regional Office, Monday-Friday, 8:00 a.m.–5:00 p.m. https://www.tceq.texas.gov/agency/directory/region/reglist.html
Maintenance Facility
Maintenance facilities accommodate needs such as office, lunch or break rooms for staff, equipment and supplies storage, and mechanics areas. All areas should be properly ventilated and well-lit. Numerous activities should be considered to help contribute to water, energy, and cost reductions:
Restrict water flow to the maximum necessary for adequate use
Use automatic shutoffs on faucets
Install 1.5-gallon tanks on toilets
Use motion detectors to turn on lights when staff is present
Administrative and Managerial Offices, Employee Break Room and Training Area
Maintenance facilities should include an employee lunch/break room, which can also serve as a professional training area for technical education. The area should be clean, organized, and promote a relaxed atmosphere. The size of the lunchroom will be determined by the size of the golf course operation and number of maintenance crew employees; this area should be developed alongside the administrative and managerial offices with desks, computers, files, phones, and storage. Important items to include:
Ample tables/chairs for dining and training
One or two microwave ovens (reduces time for meal preparation)
One adequate-sized (energy saver) refrigerator
Drinking water with dispenser, coffeemaker, refreshment vending machine
Kitchen area with sink, water, sufficient cabinet area
Adequate space including light, easy-to-clean colors/walls
Organized food and utensil storage with labeled containers and easy-to-access shelves
Erasable or electronic communication board
Air conditioned and insulated, with overhead fans for air flow
Employee Restroom/Locker Room/Shower
Design restrooms to promote superior personal hygiene. They should be easy to clean with adequate space/amenities to service several employees simultaneously. The locker room should be adjacent to restrooms and incorporate full-length lockers with at least one shower. Use a semi-gloss, high quality paint for ease of cleaning. Use a dry deck type material on portions of the floor to prevent slippage and spread of bacteria. These rooms should be insulated and air conditioned
Mechanics Workshop and Office
The mechanics workshop should be designed with enough space to facilitate servicing and repair of equipment. To minimize the risk of injuries, install an assortment of lifts (beam supported, flush floor mounted, and portable) which should be used to assist with moving equipment. Floor space requirements can be reduced through installing grease and oil dispensers in an overhead lube center, supported by compressed air connected to bulk drums. Inflammable materials should be kept in fire resistant storage and a sink and hand dryer should be available for staff use.
Large work benches provide ease for working at waist level and can decrease risk of back injury. These benches can also incorporate underneath storage for space optimization. An air-conditioned office with desk, computer, files, phone, and storage should be adjoining.
Storage Areas
Chemical and Fertilizer Storage
Due to their potentially hazardous nature pesticides should be stored inside an IPM Control Center. This is a lockable concrete or metal building designed for storage of pesticides which should be located away from other buildings, especially fertilizer and fuel storage facilities.
A separate fertilizer storage structure should be large enough to allow a small forklift to deliver fertilizer by pallet. If the building is constructed of metal this should be protected from degradation by fertilizer (such as adding painted plywood around the walls). A dehumidifier can be a useful addition to a fertilizer tool in order to help protect fertilizer from water absorption.
Best Management Practices
Place appropriate warning signs within and outside of storage buildings.
Store PPE away from pesticide storage in an easily accessible area.
Follow all PPE statements on pesticide labels.
Develop an emergency response plan and educate personnel regarding emergency procedures on a regular basis.
Individuals conducting emergency chemical cleanups should be properly trained under requirements of the Occupational Safety and Health Administration (OSHA).
Detailed records of current pesticide inventory should be maintained in the storage facility.
SDS for chemicals stored onsite should be readily accessible and stored separately from the storage room.
Follow a “first in, first out” principle to rotate products into use and ensure products do not expire. Do not store large quantities of pesticides or chemicals for long periods.
Store chemicals in original containers; never store in containers that might be mistaken as packaging for food or drink.
For more information refer to the Pesticide Management Section for additional BMPs.
Soil Storage
Soil storage and fertilizer storage areas should be near to each other. Deliveries may be deposited outside storage bins and pushed into the bin with a front-end loader. Soil storage areas should have roof coverings to prevent wind from dispersing seeds into top dressing and to prevent rain or moisture from reaching the soil.
Block walls that separate sand, topdressing, and rock should be filled solid with concrete. Ceiling fans can help reduce moisture retention.
Equipment Maintenance & Storage
Equipment storage and maintenance facilities should be designed to prevent accidental discharge of chemicals, fuels, or contaminated wash water from reaching water sources. The proper storage and preventive maintenance of equipment also extends the useful life of machines and reduces repairs. The equipment maintenance and storage areas provide an excellent location for the shop compressor, eliminating the loud running sound in a personnel work area.
Developing a list of necessary equipment to properly maintain the golf course, with information including the size of the equipment is important to determine space requirements. Each piece of equipment should have a designated spot, delineated by colored lines, with its name or number indicated, and consistently parked in the same spot daily. It helps to identify if a leak (oil, hydraulics, etc.) develops when equipment is parked in a designated location and increases accountability for optimal operating conditions.
Good facility logistics planning and management will minimize unnecessary shuffling of equipment when one piece needs to be brought in or out. Overhead doors located on both sides of the equipment storage area allow for ease when moving equipment and improve air flow. Overhead fans in the equipment storage area facilitate also air flow and help reduce moisture.
Waste oil from equipment should be collected and stored in a container set on containment. If stored outside, there should be a roof over the container and a valve in the bottom to release rainwater.
Best Management Practices
Store and maintain equipment in a covered area with a sealed impervious surface to limit risk of fluid leaks and facilitate early detection of small leaks that may require repair.
Seal floor drains unless they are connected to a holding tank or sanitary sewer with permission from the local wastewater treatment plant.
Store pesticide and fertilizer application equipment in areas protected from rainfall to prevent discharge into soil or water.
Store solvents and degreasers in lockable metal cabinets away from ignition sources in a well-ventilated area. These products are generally toxic and highly flammable. Never store them with fertilizers or in areas where smoking is permitted.
Keep an inventory of solvents and SDS for materials onsite, in a different location that is easily accessible in case of an emergency.
Keep basins of solvent baths covered to reduce emissions of volatile organic compounds.
When possible, replace solvent baths with recirculating aqueous washing units. Soap and water or other aqueous cleaners are often as effective as solvent-based products and present a lower risk to the environment.
Always use appropriate PPE when working with solvents.
Never allow solvents or degreasers to drain onto pavement or soil, or discharge into waterbodies, wetlands, storm drains, sewers, or septic systems.
Collect used solvents and degreasers in containers clearly marked with contents and date.
Blow off equipment with compressed air to reduce damage to hydraulic seals.
Equipment Washing
A clean, enclosed, watertight area should be dedicated for washing down equipment. Closed loop water recycling systems with a proven track record should be utilized. Captured wash water may be pumped into a rinsate storage tank for use in the next application and used as a dilute pesticide per label instructions. Equipment washing guidelines should be established to help prevent potential for residues (such as pesticides, oil, and grass clippings) from reaching surface waters, groundwater, drainage pipes, or storm sewers.
When washing mowers, it is important to address grass clippings so that these do not enter the wash water recycling system. Blow clippings off mowers using compressed air, to be collected and composted or disposed of in a designated debris area.
For equipment with possible pesticide residue, BMPs should be followed to ensure that wash water does not become a pollution source.
Best Management Practices
Before washing use compressed air to blow off grass clippings from equipment.
Wash equipment on a water-resistant surface (concrete or asphalt pad) that collects the wash water. Once collected material dries, dispose properly.
Only use the amount of water required - wash equipment with a bucket of water and a rag; use spring-loaded spray nozzles; and minimize unnecessary rinsing.
Minimize use of detergents and use only those which are biodegradable, non-phosphate.
Consider a closed-loop wash water recycling system.
Do not discharge wash water to surface water, groundwater, or susceptible/leachable soils either directly or indirectly through ditches, storm drains, or canals; never discharge to a septic tank.
Never discharge wastewater to a sanitary sewer system without written approval from the appropriate entity.
Washing areas for equipment not contaminated with pesticide residues should drain into oil/water separators before draining into sanitary sewers or holding tanks.
Do not wash pesticide-application equipment on pads with oil/ water separators. Do not wash near wells, surface water, or storm drains.
Do not wash equipment on a pesticide mixing and loading pad; keep grass clippings and debris from becoming contaminated with pesticides.
Solvents and degreasers should be used over a basin that collects used material.
Waste Handling
Proper waste management is important for the health and safety of the public, in addition to conserving natural resources within the state of Texas. Current statewide recycling efforts include around 23 percent of waste being diverted from Texas landfills annually. TAC Title 30 §328.13 sets a recycling goal of 40 percent of municipal solid waste for the state. Waste reductions through recycling and composting result in reduced energy use and pollution. A golf course maintenance facility generates a variety of waste materials including fluorescent or LED lights, glass containers, plastic, tires, metal, paper products, solvents, chemical containers, batteries, used oils, used or contaminated fuel, paints, aluminum cans, and wood. A proper recycling and waste removal program should be deployed to maintain health and safety, plus reduce waste to landfills.
Recycling: Paper, Plastic, Aluminum, Glass, and More
Paper, cardboard, #1 and #2 plastics, aluminum, and glass should be recycled. Containers for recycling aluminum cans and plastic bottles should be placed in convenient locations on the golf course. Texas law requires television and computer-equipment manufacturers to offer recycling opportunities to consumers for these electronics. Options under the Texas Computer Recycling and TV Recycling programs for recycling electronics: https://www.tceq.texas. gov/p2/recycle/electronics/manufacturer-list.html
The waste disposal area should be located away from normal employee activity, but close enough to be utilized properly. Proper access for waste pick-up vehicles should be incorporated into the design and location.
Reference additional information:
https://www.tceq.texas.gov/p2/recycle
https://www.tceq.texas.gov/assets/public/comm_exec/pubs/gi/gi-288.pdf
Texas Waste Management Regulatory Resources
Waste Management Requirements and Permits including Dredge or Fill Material: https://www.tceq.texas.gov/permitting/waste_permits
Industrial and Hazardous Waste:
https://www.tceq.texas.gov/permitting/registration/ihw/Am_I_Regulated.html
https://www.tceq.texas.gov/assets/public/comm_exec/pubs/rg/rg-086.pdf
Composting and mulching guidance:
https://www.tceq.texas.gov/p2/composting.html
For emergency (only) information on hazards or actions to take in the event of a spill, call CHEMTREC, at (800) 424–9300. CHEMTREC is a service of the Chemical Manufacturers Association. For information on whether a spilled chemical requires reporting, call the CERCLA/RCRA help line at (800) 424–9346.
Pesticide Containers
Under the federal Resource Conservation and Recovery Act, or RCRA, a pesticide container is not empty until it has been properly rinsed. Unless properly rinsed empty a pesticide container us therefore classified as hazardous waste. Federal law (FIFRA) requires pesticide applicators to rinse all empty pesticide containers before taking other container disposal steps. The improper disposal of a hazardous waste can result in fines and/or criminal penalties. Pesticide containers that have been properly rinsed can be handled and disposed of as nonhazardous solid waste.
Resource for recycling empty, clean plastic pesticide containers: http://www.usagrecycling.com/
Reference the “Pesticide Management” section for additional BMPs for waste generated from pesticide activities.
Used Oil, Antifreeze, and Lead-Acid Batteries
Collect used oil, oil filters, and antifreeze in separate marked containers and recycle them. Oil filters should be drained (puncturing and crushed) and transported to a place that recycles used oil or to a hazardous waste collection site. Antifreeze must be recycled or disposed of as a hazardous waste using commercial collection services. Do not mix used oil with used antifreeze or sludge from used solvents.
Used-acid from lead-acid storage batteries is hazardous waste. They must be disposed of as hazardous waste, unless the acid is contained within a battery being recycled. Make sure caps are in place to contain the acid and store batteries on an impenetrable surface, under cover if possible. Used lead-acid batteries must be recycled to be exempt from hazardous waste regulations. Refer to TAC Title 30 §328.13 for additional state information regarding disposal.
Best Management Practices
Measure waste levels and implement source reduction practices to reduce the amount of waste generated in the first place.
Separate and label designated areas for recyclables and waste.
Educate staff and guests on items which may be recycled; identify ways to increase recycling efforts, including proper signage and communications.
Operate equipment properly, adhering to preventive maintenance and manufacturer guidelines to avoid need for repair and prolong lifecycle, minimizing replacement needs.
Source environmentally preferred products when possible.
Reduce waste by only purchasing materials in a quantity that can be used prior to the expiration date or within six to 12 months of purchase.
Label containers for the purpose of storing oils, solvents, degreasers, and fuels.
Never dispose of waste down storm drains.
Collect used oil, oil filters, and antifreeze in separate marked containers and recycle them as directed by local and state authorities. Antifreeze may be considered hazardous waste by state or local laws and should be handled accordingly. Commercial services are available to collect and recycle antifreeze.
Properly manage used batteries and fluorescent bulbs as Universal Waste and recycle as soon as feasible.
Recycle used tires.
Consult an expert in composting for optimal design and processes.
Utilize DNR guidelines for hazardous waste disposal and collection services.
Local laws and regulations related to disposal of hazardous waste products may vary; become familiar with local laws related to disposal/recycling of these materials.
Composting
Composting can reduce the amount of grass clippings and debris, such as leaves, or routine, healthy landscape trimmings that would normally go to a landfill. Composted materials can be used effectively to improve the soil for topdressing, non-putting surface areas, and donated or sold to offsite vendors.
In addition, the clubhouse food and beverage department may engage in food waste composting. Additional information on composting in Texas: https://www.tceq.texas.gov/p2/composting.html
Solvents and Degreasers
EPA and FDEP can deem a “small quantity generator” of hazardous waste based on disposal of as little as 25 gallons per month of used solvents, triggering regulatory reporting requirements. This is because, over time, routine discharge of small amounts of solvents can create environmental and liability consequences, due to accumulation of contaminants in soil or ground water. As much as is possible, replace solvent baths with recirculating aqueous washing units (which resemble heavy-duty dishwashers). Soap and water or other aqueous cleaners may be as effective as solvent-based ones.
Best Management Practices
Use compressed air to blow off equipment instead of washing with water to minimize wear to hydraulic seals and lead to fewer oil leaks.
Solvents and degreasers are generally toxic and highly flammable and should be stored in lockable metal cabinets in an area away from ignition sources, provided with adequate ventilation.
Never store solvents or degreasers with pesticides or fertilizers, or in areas where smoking is allowed.
Keep basins or cans of solvent covered to reduce emissions of volatile organic compounds and fire hazards.
Follow OSHA signage requirements.
Ensure all personnel wear adequate PPE, especially eye protection, when working with solvents.
Never allow solvents to drain onto pavement or soil, or discharge into waterbodies, wetlands, storm drains, sewers, or septic systems.
Most solvents can be filtered and reused so should be used over a collection basin or pad that collects all used material.
Keep an inventory of solvents stored and the SDS for each on premise, but not in the solvent storage area.
Emergency response equipment recommended by the solvent manufacturer should be kept in an easily accessible place near the storage area, but not inside the area itself.
Store collected material in marked containers until it can be recycled or legally disposed of. Solvent disposal organizations provide solvent washbasins that drain into recovery drums and pickup service to recycle or properly dispose of drum contents.
Collect used solvents and degreasers, place them into containers marked with contents and date, prior to pick up. Never mix used oil or other liquid material with used solvents. Use only FDEP-approved, licensed contractors.
Fuel Facilities
Fueling facilities should be designed, constructed, maintained and monitored to local or state codes. Check codes for regulations on storage tanks; aboveground storage tanks (AST) are the preferred storage method because it is easier to monitor for leakage. An underground storage tank (UST) must have leak detection monitoring for compliance. Leaks or spills must be contained or cleaned up immediately.
Proper fueling sites have impervious surfaces, spill containment and recovery facilities, located away from surface waters and water wells. Floor drains should be eliminated or removed unless they drain to containment storage tanks or pits.
Title 40, Section 112 of the Code of Federal Regulations (CFR) requires a Spill Prevention Control and Countermeasure (SPCC) plan for facilities with total aboveground petroleum product storage (i.e., new oil, used oil and fuel) capacity in excess of 1,320 gallons. SPCC plans can help minimize the potential for a petroleum leak or spill to occur and mitigate environmental impacts. SPCC regulations generally require secondary containment for filling and dispensing operations; alternatives are allowed if secondary containment is impractical.
Fuel Storage Requirements and Regulations
Federal: EPA
Texas: TCEQ
https://www.tceq.texas.gov/permitting/registration/pst/Am_I_Regulated.html
Best Management Practices
Locate fuel storage tanks above ground, on impervious surfaces under roofed areas, when possible.
Areas should be equipped with spill containment and recovery facilities.
Keep a log of fuel added and discharged.
Visually inspect the tank for leaks and document in an inspection log.
Place automatic shut off valves away from the tanks in case of emergency.
Post “No Smoking” signs near the fueling facility.
Properly and clearly label fuel storage tanks.
Labor & Staffing
Golf courses in Texas drive economic impact through workforce development and job creation. Texas golf course maintenance departments provide full-time and seasonal work for a diverse workforce across the state, collaborating with local municipalities, school systems, workforce development boards, and community programs to hire talented, dedicated staff.
To ensure a continuous, quality labor supply it is important to engage with state educational institutions. This can be done in a number of ways including supporting scholarships for local college students or hosting field trips for elementary, junior high, and high schools to explore golf courses from a science, math, biology, and learning perspective. These engagements begin to develop future generations of golf maintenance professionals. Superintendents frequently hire students from local schools and universities for full-time or part-time employment and internships.
Labor supply is influenced by demographic, economic, technological, educational, and societal factors. BMPs provide strategies for overcoming labor shortages and minimizing training and recruiting costs, plus lowering turnover and associated expenses. As part of the overall effort, it is crucial to create a culture of inclusiveness, teamwork, education, and professional development.
It is essential to maintain compliance with all equal rights labor standards and civil rights. Educate staff and encourage awareness of state and federal laws regarding key issues such as minimum wage regulations. OSHA training and safety practices should be kept up-to-date; accessible operating standards should be available; and proper workplace injury reports, along with clearly documented worker’s compensation programs should be in place.
Best Management Practices
Adhere to federal and state hiring regulations and requirements
Provide ongoing OSHA and safety training, post required signage
Communicate written operating standards in multiple languages and through various formats
Educate on PPE and proper safety precautions when operating equipment or handling chemicals
Understand current golf maintenance labor data, including expenses, retention, and turnover rate
Develop relationships within the community through a variety of school and government-based programs to diversify workforce
Utilize multiple recruiting methods and pipelines to integrate diversity and inclusion into hiring practices
Sponsor events, host meetings with key community influencers including school administration, chambers of commerce, parents
Utilize the Work in Texas site to post positions: https://www.workintexas.com/vosnet/Default.aspx
Understand and explore H2B process for seasonal employees
Create a statewide Apprenticeship program with unified standards that can be adopted at the facility level; where students may take courses related to the profession as a way of enhancing what is being learned on the job
Develop relations with the local school systems, vocational schools, community colleges, and universities; provide continuing education opportunities
Build relationships with post-secondary institutions to offer continued education and training through certificate programs, 2- and 4-year programs and masters programs
Recruiting Resources
There are several ways to improve the efficiency of recruitment processes, while increasing inclusivity and quality of candidates. Use a structured approach throughout recruitment – from advertising, through interviewing, all the way to onboarding. Encourage potential applicants who have faced barriers to employment and actively work to recruit appropriate candidates. Vocational rehabilitation and veteran-based programs are two widely available sources of diverse candidate pools, as are JobCorps and ex-offender programs.
Identify potential employee candidates using:
Chamber of Commerce
Ex-Offender programs
H-2B
Public workforce systems
Retirees
School systems
Staffing agencies
Veteran-based programs
Vocational rehabilitation
Understanding Golf Course Labor Data
Understanding local data around workplace culture, barriers, and operational data is important when developing a recruitment and labor management plan. Conduct an operational audit through a third party or input data from monthly tracking systems including digital job boards, GPS tracking systems, time studies, and other performance metrics such as engagement surveys. Once annual data is entered, it should be designated as the baseline year to measure against in subsequent years.
Public Workforce Systems: Local Workforce Development (LWD) Boards
A Workforce Development Board is a group of community leaders appointed by local elected officials and charged with planning and oversight responsibilities for workforce programs and services in their area. In Texas, there are 28 LWDs which help employers recruit, develop on-the-job training and financial reimbursement programs, and provide access to job fairs and job seekers.
Additional Information:
https://www.twc.texas.gov/partners/workforce-development-boards-websites
Vocational Rehabilitation
The Texas Vocational Rehabilitation Services supports people with disabilities to prepare for, obtain and advance in meaningful employment. This no cost program provides additional talent pipelines to recruit qualified workers, build diversity, connect golf courses to experts on the American Disabilities Act, and to access workforce planning resources.
Additional information:
https://www.twc.texas.gov/programs/vocational-rehabilitation-program-overview
Veteran Programs
The Texas Workforce Commission and Texas Veterans Commission serve to encourage employers to build a workplace support system for veterans, hire and retain more veterans, and connect to veterans in the community and their families. These organizations maintain a list of employers with written veteran hiring policies or initiatives, this provides awareness to encourage applicants and recognition. The HIRE Vets Medallion Award may be applied for to show commitment to veteran hiring, retention, and professional development.
Additional information:
https://www.twc.texas.gov/businesses/hiring-veterans
https://www.tvc.texas.gov/employment/employers/
School Systems
Reaching out to guidance counselors, work-study, and co-op coordinators is an effective method to reach students. Volunteering for career awareness programs as early as kindergarten will help build relations. Also connect with career and technical education programs or centers.
Additional information:
https://tea.texas.gov/academics/college-career-and-military-prep/career-and-technical-education
Additional information:
https://www.twc.texas.gov/partners/workforce-development-boards-websites
Chambers of Commerce
There are 510 Chambers of Commerce in the state of Texas. These organizations provide exceptional networking opportunities for golf course superintendents to share employment opportunities, participate in outreach events, and conduct meet-and-greets. These organizations can provide opportunities to meet with influencers in the community, civic organizations (Rotary, Kiwanis, Lions), and industry-centric conferences as well.
Additional information:
The H2B Temporary Workers Program & Process
The H-2B temporary non-agricultural program allows U.S. employers who meet specific regulatory requirements to bring foreign nonimmigrant workers to the U.S. to fill temporary nonagricultural jobs. Before requesting H-2B classification from the U.S. Citizenship and Immigration Services (USCIS), the employer must apply for and receive a temporary labor certification for H-2B workers from the U.S. Department of Labor (DOL).
Step 1
Employer Obtains a Prevailing Wage Determination (PWD) from the National Prevailing Wage Center (NPWC) using the Application for Prevailing Wage Determination (ETA Form 9141) PWD may also be submitted by mail to the following address:
U.S. Department of Labor
Employment and Training Administration
Office of Foreign Labor Certification
National Prevailing Wage Center
1341 G Street, NW- Suite 201
Washington, DC 20005- 3105
ATTN: PWD Request
Step 2:
Employer Conducts Pre-Filing Recruitment: File a job order no more than 120 calendar days prior to the employer’s date of need with the State Workforce Agency (SWA) serving the area of intended employment. The job order must be open and available for recruitment purposes for a minimum of 10 days. The list of SWA contacts can be found here.
Publish two print advertisements for the position(s), one of which must be on a Sunday. Advertisements must be placed during the period of time the job order is active. Job order and print advertising must contain:
Employer’s name and contact information to allow applications to send resumes
Geographic area of employment to allow applicants to be aware of travel requirements and where applicant will likely have to reside to perform the services or labor
If transportation to the worksite is provided by the employer, the advertising must say so
Description of job opportunity including duties to apprise applicants of services or labor to be performed and the duration of the job opportunity
Work hours and days, expected start and end dates of employment, and whether or not overtime will be available
Wage offer or offers in the event of multiple wage offers
Disclose the position is temporary, and the total number of job openings the employer intends to fill
Step 3:
Employer submits an application and provides the following documentation to the Chicago National Processing Center (NPC):
Completed ETA Form 9142B, https://www.dol.gov/sites/dolgov/ files/ETA/oflc/pdfs/ETA_Form_9142B.pdf - Application for Temporary Employment Certification
Completed ETA Form 9142 - Appendix B https://www.dol.gov/sites/dolgov/files/ETA/oflc/pdfs/ETA_ Form_9142B_APPENDIX.pdf
Completed recruitment report
Any applicable supporting documentation (documentation substantiating temporary need is recommended)
Electronic Filing:
Employers may submit the H-2B application electronically via the Department's iCERT Portal System. Read the H-2B iCert Quick Start Guide and H-2B iCERT User Manual before completing and submitting an H-2B application. The online help provides step-by-step instructions for completing and submitting the H-2B application electronically. For resources and information, visit: http://www.foreignlaborcert.doleta.gov/h2ah2b_icert_rollout.cfm
Mail Filing:
Mail the application package to the Chicago NPC at:
U.S. Department of Labor
Employment and Training Administration
Office of Foreign Labor Certification
Chicago National Processing Center
11 West Quincy Court
Chicago, IL 60604- 2105
ATTN: H-2B Program Unit
Additional H2B information:
https://www.foreignlaborcert.doleta.gov/h-2b.cfm
Source: Wisconsin Golf Course Best Management Practices Guide, 2020
Apprenticeships
Another way to broaden the profile of applicants and find the best candidate is to consider providing apprenticeship opportunities. Under apprenticeships employees are provided with instruction and on-the-job training. The training is much more customizable than traditional tertiary education systems and can be tailored to fit employer needs.
High school juniors and seniors can bring new talent to a golf course team through one or two-year youth apprenticeships. During these apprenticeships, students complete relevant courses aligned to enhance what is being learned on the job. Through these programs young people can develop skills and start on the path toward becoming credentialed workers, or work toward college credit programs.
Additional information: https://www.twc.texas.gov/programs/apprenticeship-program-overview
Continued Education
Connect with local institutions and community colleges to learn about services and potential collaboration for workforce development. There may be grant programs available. Be flexible and help employees with on-the-job training, whether through internal or external programs. The following post-secondary institutions offer turfgrass, landscape, or horticulture programs:
Western Texas College
6200 College Avenue
Snyder, TX 79549
https://www.wtc.edu
Texas Tech University
Texas Tech Plaza
1901 University Avenue, Suite 513
Lubbock, Texas 79410-5095
http://www.depts.ttu.edu
North Central Texas College
1525 West California Street
Gainesville, TX 76240
https://www.nctc.edu/
Texas A&M University
2474 TAMU
College Station, TX 77843
https://soilcrop.tamu.edu/